The Brownie Process
Pre-Construction
-
Brownie Construction thrive on Early Contractor Involvement and enjoy being able to assist with build-ability. We want to build a strong relationship with the design team this ensures the architect and engineer can have trust in Brownie Construction to deliver the intended design.
Our pricing is extremely competitive due to the relationships we have built with sub-contractors and merchants, helping to secure the best possible market rates.
-
The market has experienced significant increases, and Brownie Construction are mitigating this as much as possible by securing stock early. We often procure key items like frames and trusses early to ensure that we can meet programme requirements and lock in rates.
-
We have found the market has settled currently and we are not experiencing the same increases. We will not get complacent with this as we know this can change in an instant. Early procurement is key to locking in rates with supply. We will potentially look at early procurement and storage of some high-risk items to ensure we don’t have escalation as this can add significant costs to a project.
-
Once we have a signed contract we will look to arrange fixed pricing from our major suppliers. This will make a major difference to minimise escalation of costs.
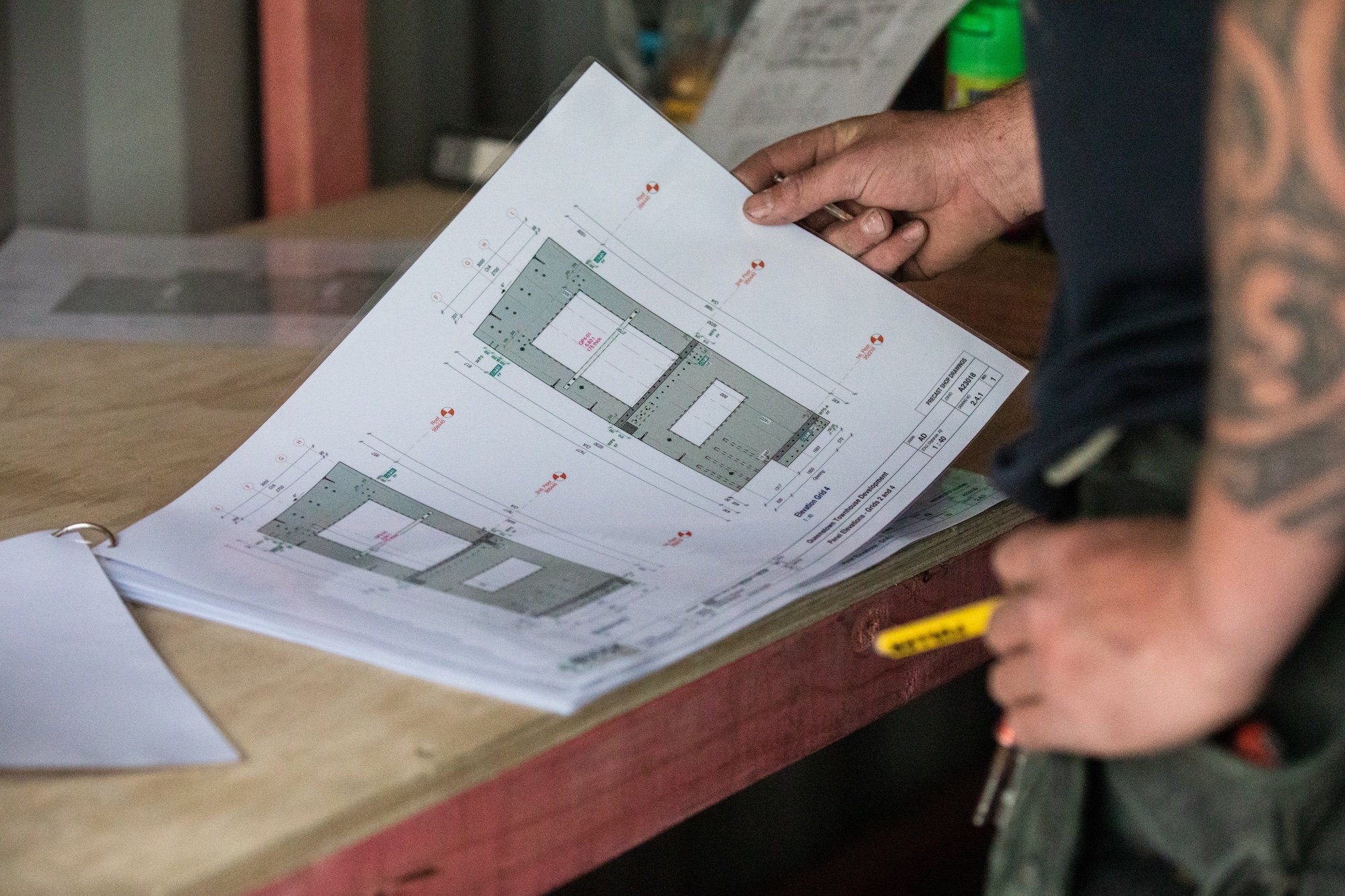
Construction
-
Our diversely skilled team gives us a wealth of knowledge we can draw from at any time. From big to small, residential to commercial jobs, we have you covered.
-
From a client decision perspective, we will run a clear RFI process with instructions provided and tracked on spreadsheets run by our project administrators. This means we will not get to a point on site where works must stop because we haven’t had a decision made. These will be reported on monthly so we as a project team can make sure that works on site are not held up.
Planning is key to the success of a project of this scale. Our team run Last Planner, they plan 2 month ahead of time to ensure that materials and subcontractors are on site and are well informed.
-
We have a quality management software that we use throughout the build. These are project specific and means that we can capture quality issues as they arise rather than waiting until they are too late to fix. This is important not only for ensuring we deliver a high-quality product, but also to manage programme. We can lose a lot of time on site fixing issues that were not picked up along the way.
-
We have a robust health and safety system in place. This is managed site by site specifically as every site has different risks and how we control these. We have a site-specific safety management plan, in this project case this will tie in with the environmental management plan as well. We then manage specific risks on site with JSA/Task Analysis. There will be significant risks on site including heavy machinery, cranes, scaffolding and working at heights being the highest risk. We also manage our hazard/incident reporting through this software.
No matter how big or small the incident is these incidents are reviewed by our site managers and project admin. If we find trends within these incidents this allows the team to put in controls for these risk across all our sites.
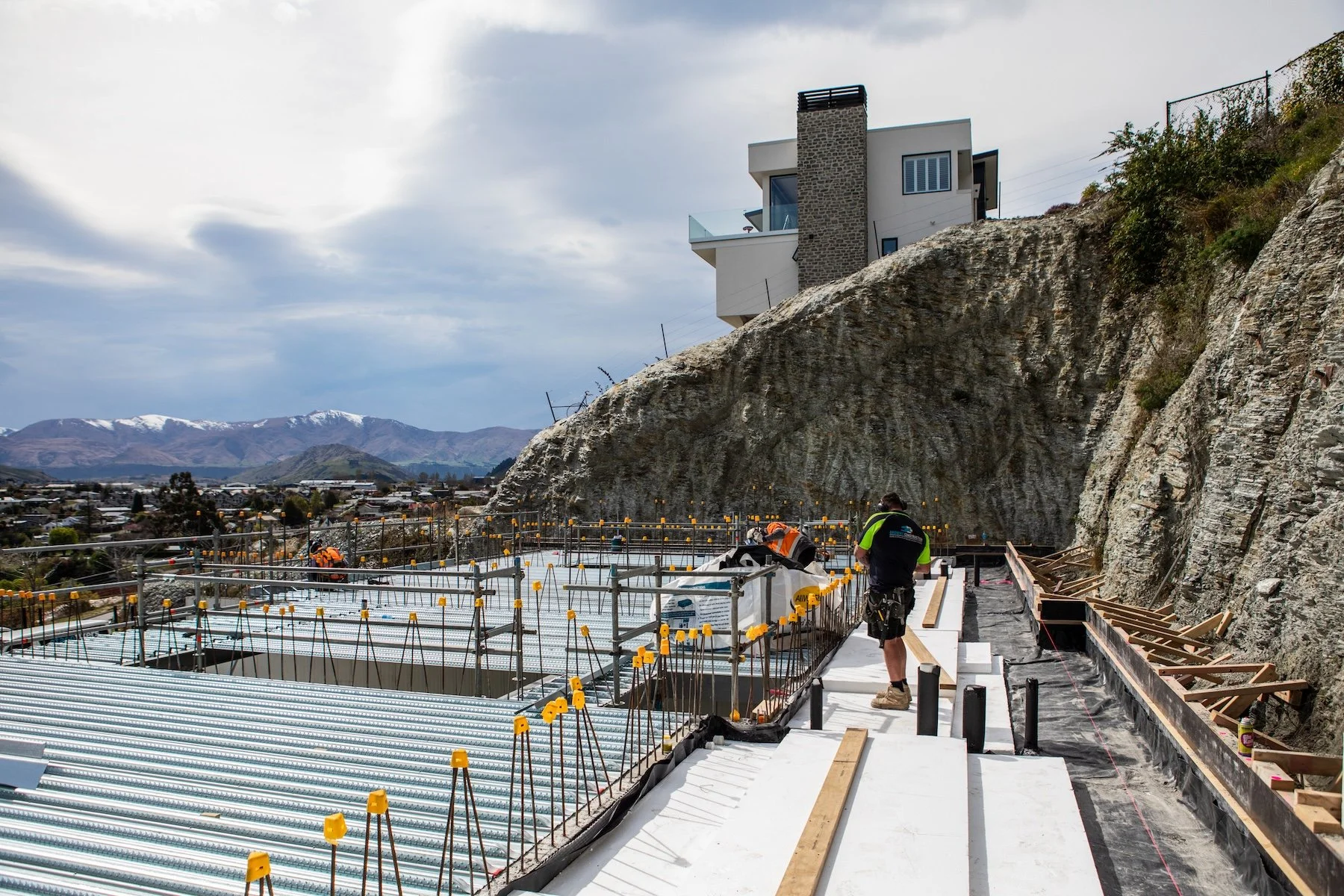
Completion
-
As deadlines draw near and final compliance is organised, it can be a stressful time. Brownie Construction are proactive with the management of this and arrange completion documents for consultants and the Council throughout the construction phase. This ensures we can achieve prompt consultant sign off and Council Compliance to meet handover. Inspections are conducted throughout the build process and extensive final defects inspections occur at build completion to ensure quality standards have been maintained and that there are minimal issues at handover.
-
We will ensure that Brownie Construction conducts detailed quality inspections prior to the client or architect walks through on their defect inspection. This will minimise the number of quality issues picked up at this point. Ensuring that there are no or minimal minor defects when the clients move into the home.
If there are outstanding defects or deferred works, these will be monitored by our Project Manager and Project Administrator so we can address these defects in a timely manner to minimise tradesmen working in the home after our clients have moved in.
